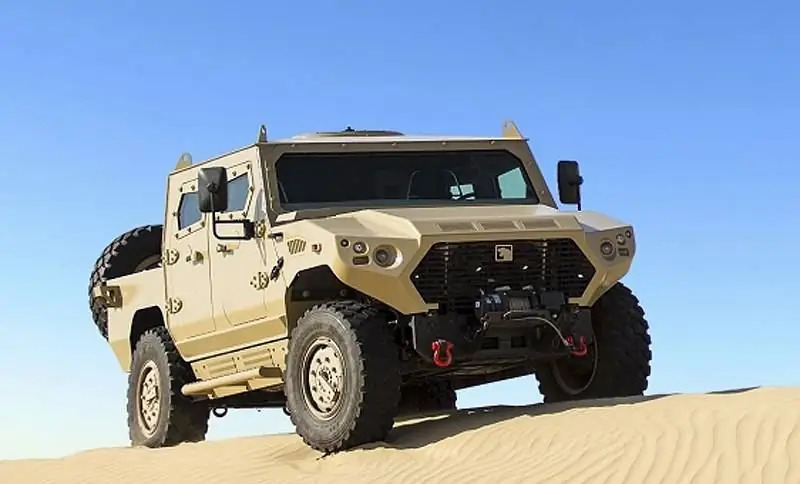
Armor on miljoneid aastaid vanem kui inimkond ja see on välja töötatud peamiselt lõualuude ja küüniste eest kaitsmiseks. Võimalik, et krokodillid ja kilpkonnad võivad inimesi osaliselt inspireerida kaitsvate elementide loomiseks. Kõik kineetilise energia relvad, olgu see siis eelajalooline klubi või soomust läbistav mürsk, on mõeldud vägevale alale suurte jõudude koondamiseks, selle ülesanne on tungida sihtmärki ja tekitada sellele maksimaalset kahju. Järelikult on soomukite ülesanne seda ära hoida, suunates ründevahendid kõrvale või hävitades ja / või löökenergia hajutades võimalikult suurele alale, et minimeerida igasugust kahju inimjõule, transpordisüsteemidele ja konstruktsioonidele, mida see kaitseb.
Kaasaegne raudrüü koosneb tavaliselt kõvast väliskihist mürsu peatamiseks, kõrvalejuhtimiseks või hävitamiseks, vahekihist, millel on väga kõrge „purunemistöö”, ja viskoossest sisekihist, et vältida pragusid ja prahti.
Terasest
Teras, mis sai esimeseks soomussõidukite loomisel laialdaselt kasutatavaks materjaliks, on endiselt nõudlik, hoolimata alumiiniumist ja titaanist kergsulamitest, keraamikast, polümeermaatriksiga komposiitmaterjalidest, klaaskiududega tugevdatud soomuste, aramiidi, soomuste tekkimisest. ja ülikõrge molekulmassiga polüetüleenist, samuti metallmaatriksiga komposiitmaterjalidest.
Paljud terasetehased, sealhulgas SSAB, arendavad jätkuvalt kõrgtugevaid terasid mitmesuguste kaalukriitiliste rakenduste jaoks, näiteks lisakattena. Soomustatud terasest klass ARM OX 600T, saadaval paksusega 4-20 mm, on saadaval garanteeritud kõvadusega 570-640 HBW ühikut (lühend Hardness, Brinell, Wolfram; test, mille käigus pressitakse standardse läbimõõduga volframkuuli teadaoleva jõuga materjali proovi, siis mõõdetakse tekkinud süvendi läbimõõt; seejärel asendatakse need parameetrid valemiga, mis võimaldab saada kõvadusühikute arvu).
SSAB rõhutab ka seda, kui oluline on saavutada kõvaduse ja sitkuse õige tasakaal läbitungimise ja lõhkemiskaitse jaoks. Nagu kõik terased, koosneb ka ARMOX 600T rauast, süsinikust ja paljudest muudest legeerivatest komponentidest, sealhulgas räni, mangaan, fosfor, väävel, kroom, nikkel, molübdeen ja boor.
Kasutatavatel tootmismeetoditel, eriti temperatuuri osas, on piiranguid. See teras ei ole ette nähtud täiendavaks kuumtöötlemiseks; kui pärast tarnimist kuumutatakse seda üle 170 ° C, ei saa SSAB selle omadusi garanteerida. Ettevõtted, kes suudavad sellistest piirangutest mööda pääseda, tõmbavad tõenäoliselt soomukitootjate hoolikat kontrolli.
Teine Rootsi ettevõte Deform pakub kuulikindlaid soomusterasest kuumvormitud osi soomustatud sõidukite tootjatele, eriti neile, kes soovivad parandada tarbe- / tsiviilsõidukite kaitset.
Üheosalised Deformi tulemüürid on paigaldatud Nissan PATROL 4x4, väikebuss Volkswagen T6 TRANSPORTER ja pikap Isuzu D-MAX koos samast materjalist tugeva põrandaplaadiga. Deformi välja töötatud ja lehtede tootmisel kasutatav kuumvormimisprotsess säilitab kõvaduse 600 HBW.
Ettevõte väidab, et suudab taastada kõigi turul olevate soomusteraste omadused, säilitades samal ajal struktuurselt määratletud kuju, samas kui saadud osad on palju paremad kui traditsioonilised keevitatud ja osaliselt kattuvad konstruktsioonid. Deformi väljatöötatud meetodi puhul karastatakse ja karastatakse lehed pärast kuuma sepistamist. Tänu sellele protsessile on võimalik saada kolmemõõtmelisi kujundeid, mida ei saa külmvormimisel ilma kohustusliku sellistel juhtudel "keevisõmblused, mis rikuvad kriitiliste punktide terviklikkust".
Deformatsiooni kuumvaltsitud terasplekke on kasutatud BAE Systems BVS-10 ja CV90 ning alates 1990. aastate algusest paljudel Kraus-Maffei Wegmanni (KMW) masinatel. Tulevad tellimused kolmemõõtmeliste soomusplaatide tootmiseks paagile LEOPARD 2 ning mitme kujuga plaatide tootmiseks sõidukitele BOXER ja PUMA, lisaks mitmele Rheinmetalli sõidukile, sealhulgas taas BOXERile, samuti luugi WIESEL sõidukile. Deform töötab ka teiste kaitsvate materjalidega, sealhulgas alumiinium, kevlar / aramiid ja titaan.
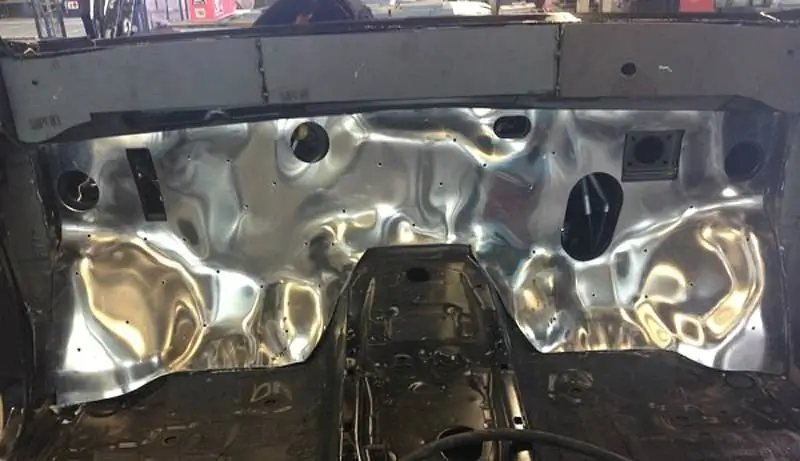
Alumiiniumi areng
Mis puutub soomukitesse, siis esmakordselt kasutati alumiiniumist soomust soomustransportööri M113 tootmisel, mida toodetakse alates 1960. aastast. See oli sulam 5083, mis sisaldas 4,5% magneesiumi ja palju väiksemas koguses mangaani, rauda, vaske, süsinikku, tsinki, kroomi, titaani jt. Kuigi 5083 säilitab oma tugevuse ka pärast keevitamist, ei ole see kuumtöödeldav sulam. Sellel ei ole nii head vastupidavust 7,62 mm soomust läbistavatele kuulidele, kuid nagu ametlikud testid kinnitasid, peatab see 14,5 mm nõukogude stiilis soomust läbistavad kuulid paremini kui teras, säästes samas kaalu ja lisades soovitud tugevust. Sellise kaitsetaseme jaoks on alumiiniumleht paksem ja 9 korda tugevam kui teras, mille tihedus on väiksem 265 r / cm3, mille tulemusel väheneb konstruktsiooni kaal.
Soomusmasinate tootjad hakkasid peagi nõudma kergemaid, ballistiliselt tugevamaid, keevitatavaid ja kuumtöödeldavaid alumiiniumist soomuseid, mis tõi kaasa selle, et Alcan arendas välja 7039 ja hiljem ka 7017, mõlemad suurema tsingisisaldusega.
Nagu terase puhul, võib stantsimine ja sellele järgnev kokkupanek negatiivselt mõjutada alumiiniumi kaitseomadusi. Keevitamisel soojust mõjutavad tsoonid pehmenevad, kuid nende tugevus taastatakse osaliselt loomuliku vananemise tõttu tekkiva kõvenemise tõttu. Metalli struktuur muutub kitsastes tsoonides keevisõmbluse lähedal, tekitades suuri jääkpingeid keevitus- ja / või kokkupanekuvigade korral. Järelikult peaksid tootmistehnikad neid minimeerima, samas tuleks minimeerida ka stressikorrosiooni pragunemise riski, eriti kui masina eeldatav kasutusiga on üle kolme aastakümne.
Stresskorrosiooniga pragunemine on pragude tekkimise ja kasvu protsess söövitavas keskkonnas, mis kipub legeerivate elementide arvu suurenemisega halvenema. Pragude teke ja nende järgnev kasv toimub vesiniku difusiooni tagajärjel mööda terade piire.
Pragunemiskindluse määramine algab pragudest väikese koguse elektrolüüdi eraldamisega ja selle analüüsimisega. Madala pingega pingekorrosioonikatseid tehakse selleks, et teha kindlaks, kui halvasti konkreetset sulamit rünnati. Kahe proovi mehaaniline venitamine toimub (üks söövitavas keskkonnas ja teine kuivas õhus), kuni need ebaõnnestuvad, ja seejärel võrreldakse plastilist deformatsiooni luumurdekohas - mida rohkem proovi venitatakse, seda parem.
Töötlemise ajal saab parandada vastupidavust pingekorrosiooni pragunemisele. Näiteks Total Materia andmetel, mis nimetab end “maailma suurimaks materjalide andmebaasiks”, on Alcan parandanud 7017 jõudlust kiirendatud korrosioonipragumiskatsetes 40 korda. Saadud tulemused võimaldavad välja töötada ka keevitatud konstruktsioonide tsoonide korrosioonikaitse meetodid, milles on raske vältida jääkpingeid. Uurimistööd sulamite täiustamiseks keevisliidete elektrokeemiliste omaduste optimeerimiseks jätkuvad. Töö uute kuumtöödeldavate sulamite kallal keskendub nende tugevuse ja korrosioonikindluse parandamisele, samas kui kuumtöötlemata sulamite kallal töötamise eesmärk on kõrvaldada keevitatavusnõuetest tulenevad piirangud. Arendatavad kõige karmimad materjalid on 50% tugevamad kui praegu kasutatavad parimad alumiiniumist raudrüü.
Madala tihedusega sulamid, näiteks liitiumalumiinium, säästavad kaalult umbes 10% võrreldes varasemate sulamitega, millel on võrreldav kuulikindlus, kuigi ballistilist jõudlust ei ole Total Materia andmetel veel täielikult hinnatud.
Samuti paranevad keevitusmeetodid, sealhulgas robotmeetodid. Lahendatavate ülesannete hulgas on soojusvarustuse minimeerimine, stabiilsem keevituskaar tänu energia- ja juhtmesüsteemide täiustamisele, samuti protsessi jälgimine ja juhtimine ekspertsüsteemide poolt.
MTL Advanced Materials töötas koos ALCOA Defense'iga, tuntud alumiiniumist soomusplaatide tootjaga, et töötada välja see, mida ettevõte kirjeldab kui "usaldusväärset ja korratavat külmvormimisprotsessi". Ettevõte märgib, et soomuste jaoks välja töötatud alumiiniumisulamid ei olnud ette nähtud külmvormimiseks, mis tähendab, et selle uus protsess peaks aitama vältida tavalisi rikerežiime, sealhulgas pragunemist. Ettevõtte sõnul on lõppeesmärk võimaldada masinaehitajatel minimeerida keevitusvajadust ja vähendada osade arvu. Ettevõte rõhutab, et keevitusmahu vähendamine suurendab konstruktsiooni tugevust ja meeskonna kaitset, vähendades samal ajal tootmiskulusid. Alustades hästi tõestatud sulamist 5083-H131, töötas ettevõte välja protsessi 90-kraadise paindenurgaga osade külmvormimiseks, mis järgnes teradele ja nende vahel, seejärel liikus edasi keerukamate materjalide, näiteks sulamite 7017, 7020 ja 7085 juurde., saavutades ka häid tulemusi.
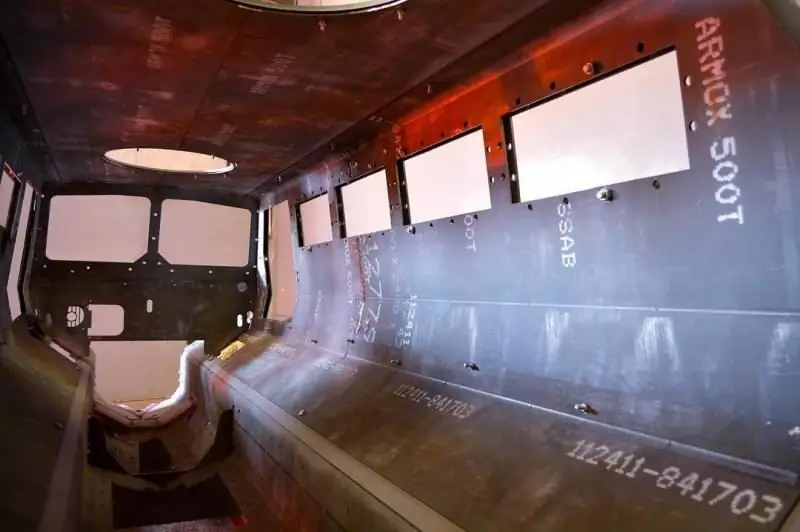
Keraamika ja komposiidid
Mitu aastat tagasi teatas Morgan Advanced Materials mitme SAMAS soomussüsteemi väljatöötamisest, mis koosnesid täiustatud keraamika ja struktuurkomposiitide kombinatsioonist. Tootesarja kuuluvad hingedega soomused, killustumisvastased vooderdised, konstruktsioonikomposiitidest valmistatud ellujäämiskapslid metallkorpuste asendamiseks ja relvamoodulite kaitsmiseks, nii asustatud kui ka asustamata. Kõiki neid saab kohandada vastavalt konkreetsetele nõuetele või tellida.
Pakub STANAG 4569 taseme 2-6 kaitset koos mitme löögiga jõudluse ja kaalu kokkuhoiuga (ettevõte väidab, et need süsteemid kaaluvad poole vähem kui sarnased terasetooted), samuti kohandumist konkreetsete ohtude, platvormide ja ülesannetega. … Killustumisvastaseid vooderdisi saab valmistada lamedatest paneelidest, mis kaaluvad 12,3 kg, et katta pindala 0,36 m2 (umbes 34 kg / m2), või tahketest liitmikest, mis kaaluvad 12,8 kg 0,55 m2 (umbes 23,2 kg / m2).
Morgan Advanced Materialsi andmetel pakub täiendav soomus, mis on mõeldud uuteks ja olemasolevate platvormide moderniseerimiseks, samu võimalusi poole kaaluga. Patenteeritud süsteem pakub maksimaalset kaitset mitmesuguste ohtude, sealhulgas väikese ja keskmise kaliibriga relvade, isetehtud lõhkeseadeldiste (IED) ja raketimootoriga granaatide eest, samuti mitme löögiga jõudlust.
Relva moodulitele (lisaks õhu- ja mererakendustele) pakutakse hea korrosioonikindlusega "poolkonstruktsioonilist" soomussüsteemi, mis koos kaalu kokkuhoiu ja raskuskeskmega seotud probleemide minimeerimisega tekitab erinevalt terasest vähem elektromagnetilise ühilduvuse probleeme.
Relvamoodulite kaitse on eriline probleem, kuna need on atraktiivne sihtmärk, kuna nende väljalülitamine halvendab drastiliselt meeskonna olukorda ja sõiduki võimet tulla toime läheduses asuvate ohtudega. Neil on ka õrn optoelektroonika ja haavatavad elektrimootorid. Kuna need paigaldatakse tavaliselt sõiduki ülaossa, peaksid soomused olema kerged, et raskuskese oleks võimalikult madal.
Relvamoodulite kaitsesüsteem, mis võib sisaldada soomustatud klaasi ja ülemise osa kaitset, on täielikult kokkupandav, kaks inimest saavad selle 90 sekundiga kokku panna. Ellujäämise komposiitkapslid on valmistatud sellest, mida ettevõte kirjeldab kui "ainulaadseid sitkeid materjale ja polümeerikoostisi", need pakuvad šrapnellikaitset ja neid saab parandada.
Sõduri kaitse
3M Ceradyne'i väljatöötatud SPS (sõdurikaitsesüsteem) sisaldab kiivreid ja kaitsevarustuses olevaid sisetükke integreeritud peakaitsesüsteemi (IHPS) ja VTP (elutähtsa torsokaitse) jaoks - ESAPI (täiustatud väikerelvade kaitsetükk) komponendid - täiustatud sisestus kaitseks SPS -süsteemi käsirelvad).
IHPS -i nõuded hõlmavad kergemat kaalu, passiivseid kuulmiskaitseid ja täiustatud nüri löögikaitset. Süsteem sisaldab ka selliseid lisaseadmeid nagu komponent sõduri alalõua kaitsmiseks, kaitsevisiir, kinnitus öise nägemise prillidele, juhendid näiteks taskulambi ja kaamera jaoks ning täiendav modulaarne kuulikaitse. Leping, mille väärtus on üle 7 miljoni dollari, näeb ette tarnida umbes 5300 kiivrit. Vahepeal tarnitakse 36 miljoni dollari suuruse lepingu alusel rohkem kui 30 000 ESAPI komplekti - kaitseriietuse kergemad lisad. Mõlema komplekti tootmine algas 2017.
Ka SPS -programmi raames valis KDH Defense välja Honeywelli SPECTRA SHIELD ja GOLD SHIELD materjalid viieks allsüsteemiks, sealhulgas SPS -projekti jaoks tarnitavaks torso ja ekstreemsuse kaitse (TEP) allsüsteemiks. TEP -kaitsesüsteem on 26% kergem, mis vähendab lõpuks SPS -süsteemi kaalu 10%. Selle süsteemi jaoks kasutab KDH oma toodetes SPECTRA SHIELD, mis põhineb UHMWPE kiul, ja GOLD SHIELD, mis põhineb aramiidkiududel.
SPECTRA kiud
Honeywell kasutab patenteeritud polümeerkiudude ketramis- ja tõmbamisprotsessi, et kinnitada UHMWPE tooraine SPECTRA kiudu. See materjal on massi poolest 10 korda tugevam kui teras, selle eritugevus on 40% kõrgem kui aramiidkiul, selle sulamistemperatuur on kõrgem kui tavalisel polüetüleenil (150 ° C) ja kulumiskindlus võrreldes teiste polümeeridega näiteks polüester.
Tugev ja jäik SPECTRA materjal näitab murdumisel suurt deformatsiooni, see tähendab, et see venib enne purunemist väga tugevasti; see omadus võimaldab neelata suurel hulgal löögienergiat. Honeywell väidab, et SPECTRA kiudkomposiidid toimivad väga hästi suure kiirusega löökide korral, nagu vintpüsside kuulid ja lööklained. Ettevõtte sõnul: „Meie täiustatud kiud reageerib löögile, eemaldades löögipiirkonnast kiiresti kineetilise energia … sellel on ka hea vibratsiooni summutamine, hea vastupidavus korduvatele deformatsioonidele ja suurepärased kiudude sisehõõrdumisomadused ning suurepärane vastupidavus kemikaalidele, vesi ja UV -valgus."
Honeywell laotab oma SHIELD -tehnoloogias paralleelsed kiudkiud ja ühendab need kokku, immutades neid täiustatud vaiguga, et luua ühesuunaline lint. Seejärel asetatakse selle lindi kihid soovitud nurkade all ja teatud temperatuuril ja rõhul risti, jootetakse komposiitkonstruktsiooniks. Pehmete kantavate rakenduste jaoks lamineeritakse see kahe õhukese ja painduva läbipaistva kile vahel. Kuna kiud jäävad sirged ja paralleelsed, hajutavad need löögienergiat tõhusamalt kui siis, kui need oleksid kootud kangasse.
Short Bark Industries kasutab SPS TEP süsteemi BCS (Ballistic Combat Shirt) ihukaitses ka SPECTRA SHIELDi. Short Bark on spetsialiseerunud pehmele kaitsele, taktikalistele rõivastele ja aksessuaaridele.
Honeywelli sõnul valisid sõdurid nendest materjalidest valmistatud kaitseelemendid pärast seda, kui nad näitasid oma aramiidkiust kolleegidega võrreldes suurepärast jõudlust.